L'Evoluzione del Manifatturiero: Un'Analisi Approfondita delle Tecnologie dell'Industria 4.0
ing.Gianluca Zorzan
8/3/20246 min read
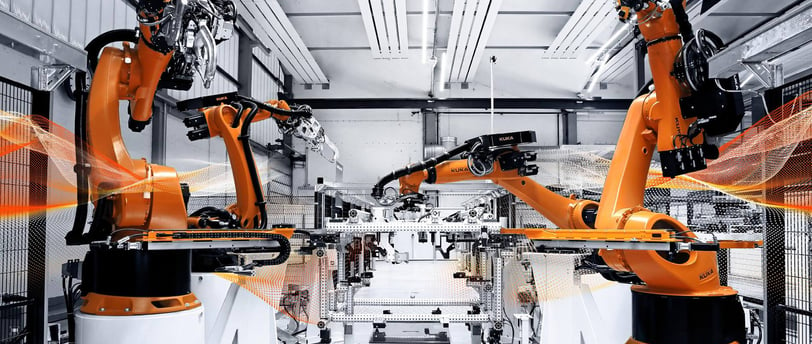
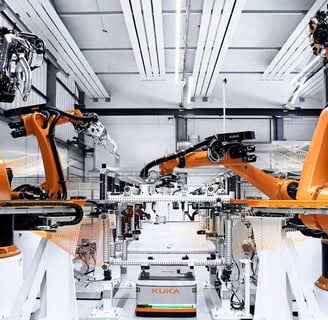
Nel cuore pulsante delle fabbriche moderne, una rivoluzione silenziosa sta ridefinendo il panorama industriale. L'Industria 4.0, con le sue tecnologie all'avanguardia, non è più un concetto futuristico, ma una realtà tangibile che sta trasformando radicalmente il modo in cui progettiamo, produciamo e gestiamo i processi manifatturieri. In questo articolo, esploreremo in profondità cinque tecnologie chiave che stanno guidando questa trasformazione, analizzando il loro impatto, le sfide implementative e le prospettive future.
1. Industrial Internet of Things (IIoT): La Rete Nervosa della Fabbrica Moderna
Immaginate una fabbrica dove ogni macchina, ogni sensore, ogni componente comunica in tempo reale, creando un flusso ininterrotto di dati. Questo è il potere dell'Industrial Internet of Things (IIoT).
L'IIoT va ben oltre la semplice connettività. Si tratta di creare un ecosistema digitale dove i dati fluiscono liberamente, permettendo decisioni informate e azioni immediate. Pensiamo a una linea di produzione automobilistica: sensori di vibrazione ultra-sensibili, capaci di rilevare variazioni minime nell'ordine di micrometri, monitorano costantemente lo stato dei macchinari. Questi dati vengono elaborati in tempo reale da sistemi edge computing, permettendo di prevedere guasti imminenti con una precisione sorprendente.
Ma l'implementazione dell'IIoT non è priva di sfide. La gestione di reti che possono includere migliaia di dispositivi, ciascuno che genera gigabyte di dati al giorno, richiede un'infrastruttura robusta e scalabile. La sicurezza, in particolare, è un aspetto critico: come proteggere questa vasta rete di dispositivi da potenziali attacchi cyber?
Nonostante queste sfide, i benefici sono innegabili. Aziende che hanno abbracciato l'IIoT riportano riduzioni dei tempi di inattività fino al 50% e aumenti di produttività che possono superare il 25%. Un produttore di componenti elettronici, ad esempio, ha ridotto i costi di manutenzione del 30% implementando un sistema IIoT per il monitoraggio predittivo.
2. Intelligenza Artificiale e Machine Learning: Il Cervello dell'Industria 4.0
Se l'IIoT è il sistema nervoso della fabbrica moderna, l'Intelligenza Artificiale (IA) e il Machine Learning (ML) ne sono il cervello. Queste tecnologie stanno portando capacità decisionali avanzate nei processi manifatturieri, analizzando enormi quantità di dati per ottimizzare ogni aspetto della produzione.
Prendiamo l'esempio di un'acciaieria all'avanguardia. Qui, algoritmi di deep learning analizzano in tempo reale dati provenienti da centinaia di sensori lungo il processo di fusione. Questi algoritmi non solo monitorano la qualità dell'acciaio, ma predicono e prevengono difetti prima che si verifichino, regolando automaticamente i parametri del processo. Il risultato? Una riduzione degli scarti del 35% e un aumento della qualità del prodotto che ha portato a un incremento del 15% nelle vendite.
L'implementazione di sistemi IA/ML nel manifatturiero, tuttavia, richiede più di semplici algoritmi sofisticati. La vera sfida sta nella preparazione e gestione dei dati. In un ambiente industriale, i dati possono essere incompleti, rumorosi o inconsistenti. La creazione di dataset robusti e rappresentativi è fondamentale per il successo di qualsiasi iniziativa di IA.
Inoltre, c'è la questione dell'interpretabilità dei modelli. In settori altamente regolamentati come l'aerospaziale o il farmaceutico, non basta avere un modello che funziona; è necessario comprendere e spiegare il processo decisionale dell'IA. Questo ha portato allo sviluppo di tecniche di "Explainable AI", che permettono di aprire la "scatola nera" dell'IA e comprenderne i ragionamenti.
3. Robotica Avanzata e Sistemi Collaborativi: La Forza Lavoro del Futuro
La robotica industriale non è certo una novità, ma l'avvento dei robot collaborativi (cobot) e dei sistemi robotici avanzati sta ridefinendo il concetto di automazione. Questi nuovi sistemi non sono solo più precisi e versatili dei loro predecessori, ma sono progettati per lavorare fianco a fianco con gli operatori umani in totale sicurezza.
Immaginate una linea di assemblaggio di elettrodomestici dove cobot dotati di sensori di forza ultra-sensibili collaborano con operatori umani. Questi robot possono "sentire" la presenza dell'operatore, adattando istantaneamente la loro forza e velocità per garantire la massima sicurezza. Allo stesso tempo, la loro precisione sub-millimetrica assicura una qualità costante nel processo di assemblaggio.
Ma la vera rivoluzione sta nella flessibilità. Sistemi robotici avanzati, programmabili attraverso interfacce intuitive o addirittura attraverso dimostrazioni fisiche, possono essere rapidamente riconfigurati per nuovi compiti. Questo permette alle aziende di adattarsi rapidamente alle fluttuazioni della domanda o all'introduzione di nuovi prodotti, un vantaggio cruciale in mercati sempre più volatili.
L'integrazione di questi sistemi robotici avanzati porta con sé nuove sfide ingegneristiche. La progettazione di celle di lavoro che ottimizzino la collaborazione uomo-robot, la creazione di interfacce utente intuitive per la programmazione dei robot, e lo sviluppo di sistemi di sicurezza avanzati sono solo alcune delle aree in cui gli ingegneri stanno spingendo i confini dell'innovazione.
4. Digital Twin: Il Ponte tra Mondo Fisico e Digitale
Il concetto di Digital Twin rappresenta forse l'esempio più emblematico di come l'Industria 4.0 stia sfumando i confini tra mondo fisico e digitale. Un Digital Twin non è una semplice rappresentazione 3D di un oggetto o di un processo; è un'entità digitale dinamica, costantemente aggiornata con dati in tempo reale, che evolve e cambia insieme al suo gemello fisico.
Pensiamo a un impianto petrolchimico complesso. Qui, il Digital Twin non si limita a replicare la geometria dell'impianto, ma incorpora modelli fisici dettagliati di ogni processo, dati in tempo reale da migliaia di sensori, e persino informazioni sul personale e sulla manutenzione. Questo "gemello digitale" permette di simulare scenari complessi, ottimizzare i processi in tempo reale e prevedere potenziali problemi prima che si verifichino.
L'implementazione di un Digital Twin a questo livello di complessità richiede un'integrazione senza precedenti di diverse discipline ingegneristiche. Esperti di modellazione 3D lavorano a fianco di specialisti di simulazione multifisica, ingegneri di processo e data scientist per creare un modello che sia non solo accurato, ma anche utile e actionable.
Le sfide sono numerose. La sincronizzazione in tempo reale tra il gemello fisico e quello digitale richiede infrastrutture di comunicazione robuste e a bassa latenza. La gestione e l'elaborazione di enormi quantità di dati richiedono potenti sistemi di calcolo, spesso basati su cloud. E poi c'è la questione della fedeltà del modello: come bilanciare accuratezza e complessità per creare un Digital Twin che sia sia preciso che computazionalmente gestibile?
Nonostante queste sfide, i benefici sono straordinari. Aziende che hanno implementato Digital Twin riportano riduzioni dei tempi di sviluppo fino al 50%, aumenti di efficienza operativa del 25% e miglioramenti significativi nella manutenzione predittiva.
5. Additive Manufacturing: Ridefinire i Limiti della Produzione
L'Additive Manufacturing, comunemente nota come stampa 3D, sta rivoluzionando non solo come produciamo, ma cosa possiamo produrre. Questa tecnologia sta spingendo i confini della progettazione e della produzione in modi che erano inimmaginabili solo pochi anni fa.
Nel settore aerospaziale, ad esempio, l'Additive Manufacturing sta permettendo la creazione di componenti con geometrie complesse che ottimizzano il rapporto resistenza-peso. Un caso emblematico è quello di un produttore di motori per aerei che ha utilizzato la stampa 3D in metallo per ridisegnare un iniettore di carburante. Il nuovo componente, impossibile da produrre con metodi tradizionali, ha ridotto il peso del 25% e aumentato l'efficienza del motore del 15%.
Ma l'Additive Manufacturing non riguarda solo la produzione di parti finali. Sta trasformando l'intero processo di sviluppo prodotto. Prototipazione rapida, tooling on-demand, e persino la produzione di parti di ricambio just-in-time stanno cambiando radicalmente i tempi e i costi dello sviluppo e della manutenzione.
Le sfide tecniche rimangono significative. La qualità e la ripetibilità dei pezzi stampati in 3D, soprattutto per applicazioni critiche, richiedono un controllo di processo estremamente preciso. La caratterizzazione dei materiali e lo sviluppo di nuove leghe ottimizzate per l'Additive Manufacturing sono aree di intensa ricerca. E poi c'è la questione della scalabilità: come portare questa tecnologia dalla produzione di piccoli lotti alla produzione di massa?
Nonostante queste sfide, l'Additive Manufacturing sta rapidamente passando da tecnologia di nicchia a strumento essenziale nell'arsenale produttivo delle aziende manifatturiere moderne.
Conclusione: Verso un Futuro Integrato e Intelligente
L'Industria 4.0 non è semplicemente l'adozione di nuove tecnologie; rappresenta un cambio di paradigma nel modo in cui concepiamo la produzione. Le tecnologie che abbiamo esplorato - IIoT, IA/ML, Robotica Avanzata, Digital Twin e Additive Manufacturing - non operano in isolamento, ma si integrano e si potenziano a vicenda, creando ecosistemi produttivi intelligenti e adattivi.
Questa integrazione porta con sé sfide significative. La gestione della complessità, la sicurezza dei dati, la formazione del personale e l'adattamento dei processi aziendali sono solo alcune delle aree che richiedono attenzione. Ma le opportunità sono altrettanto significative: aumento dell'efficienza, personalizzazione di massa, nuovi modelli di business basati sui dati, e una produzione più sostenibile e resiliente.
Per le aziende manifatturiere, la domanda non è più se adottare queste tecnologie, ma come integrarle in modo efficace e strategico. Questo richiede una visione chiara, un approccio sistemico e, soprattutto, la volontà di innovare e sperimentare.
Il futuro del manifatturiero è qui, ed è più intelligente, connesso e adattivo che mai. Le aziende che sapranno navigare questa trasformazione non solo sopravvivranno, ma prospereranno nell'era dell'Industria 4.0.
Hai bisogno di informazioni?
Prenota una call strategica gratuita
ing.Gianluca Zorzan
Consulenza per l'automazione industriale,robotica, PLC.
Contatti
Richieste
info@gianlucazorzan.com
392-2605561
© 2024. All rights reserved.