Ottimizzare la Produzione Industriale: La Guida Definitiva all'OEE
Scopri come calcolare e ottimizzare l'OEE nella tua produzione industriale. Esempi pratici, sfatiamo i miti comuni e ti mostriamo perché il 70% di OEE potrebbe non bastare.
ing.Gianluca Zorzan
10/4/20245 min read
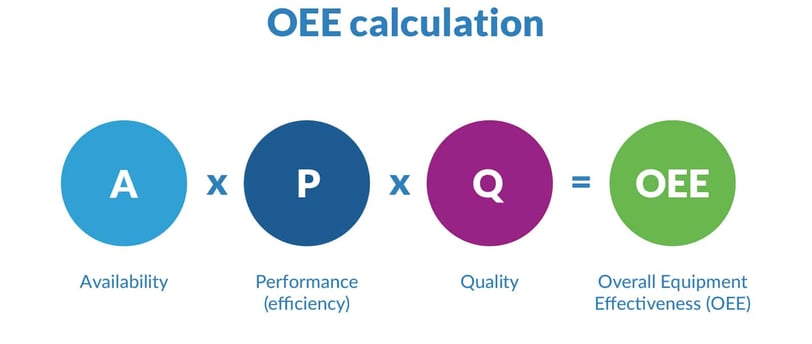
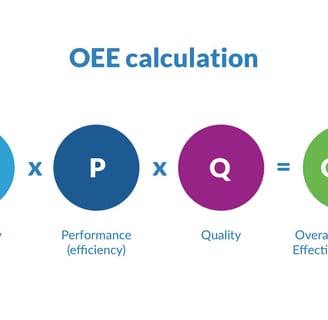
Nel mondo della produzione industriale, esiste molta confusione riguardo all'OEE (Overall Equipment Effectiveness) e ai concetti di efficienza ed efficacia. È importante fare chiarezza su questi aspetti fondamentali per comprendere il vero valore dell'OEE nel contesto produttivo.
L'OEE non è semplicemente un "bel dato da avere". Al contrario, rappresenta una mappa strategica che aiuta sia gli operatori sul campo che il management a visualizzare ed eliminare le perdite e gli sprechi nelle apparecchiature produttive. Non si tratta di una moda passeggera: l'OEE, nella sua forma elementare, esiste da decenni. I termini efficienza ed efficacia sono ancora più antichi, ma solo nell'ultimo decennio sono stati utilizzati in modo confuso e spesso intercambiabile.
Per iniziare, dobbiamo fare una distinzione chiara tra efficacia ed efficienza prima di poter discutere approfonditamente dell'OEE.
L'efficacia rappresenta il rapporto tra ciò che teoricamente potrebbe essere prodotto al termine di un processo e ciò che effettivamente viene prodotto. Facciamo un esempio concreto: se la vostra macchina è in grado di produrre 100 prodotti di qualità in un'ora, ma ne produce solo 70, allora è efficace al 70%. Tuttavia, questo dato non ci dice nulla sull'efficienza del processo, poiché non considera gli input necessari (numero di operatori, energia, materiali, etc.) per raggiungere quel 70% di efficacia.
Consideriamo uno scenario: se una macchina funziona al 50% di efficacia con un operatore e raggiunge il 65% di efficacia con due operatori, l'efficacia aumenta del 30% (sì, 65 è il 30% in più di 50), ma la sua efficienza, basata sul lavoro, si dimezza!
Lo stesso principio si applica alla resa o, come viene più comunemente chiamata, alla qualità (essenzialmente il prodotto vendibile). Nel caso dell'imbottigliamento di una bevanda, tutte le bottiglie riempite, etichettate e tappate potrebbero teoricamente essere perfette, quindi la qualità potenziale sarebbe del 100%. Ma se si scarta la metà delle bottiglie riempite a causa di difetti nel packaging o nei materiali, la resa o qualità effettiva è solo del 50%. In questo esempio, si sarebbe al 100% di efficacia ma solo al 50% di efficienza.
Un Esempio Pratico
L'OEE riguarda fondamentalmente l'efficacia: è il rapporto tra ciò che una macchina potrebbe teoricamente produrre e ciò che effettivamente produce. Il modo più semplice per calcolarlo è questo: se prendiamo la velocità massima teorica (ad esempio 60 prodotti al minuto), sappiamo che alla fine di un turno di 480 minuti dovrebbero esserci 28.800 unità.
1 turno = 8 ore = 480 minuti Velocità massima di produzione = 60 prodotti al minuto 480 x 60 = 28.800 unità
Dobbiamo poi contare quello che abbiamo effettivamente prodotto al termine del processo produttivo, come ciò che si trova sul pallet diretto al magazzino. Se ci sono solo 14.400 prodotti buoni sul pallet, l'efficacia è stata del 50%, giusto?
Fin qui niente di troppo complesso.
Gli A-P-Q dell'OEE
Perché la formula dell'OEE include disponibilità (A), prestazioni (P) e qualità (Q)? Cosa significano queste parole e quale valore aggiunto portano? Ci aiuteranno a scoprire dove sono finite le altre 14.400 unità che avrebbero dovuto essere sul pallet.
L'OEE ha alzato l'asticella, allontanandoci dal calcolo tradizionale dell'efficienza come misura dell'output della linea di produzione, che era facilmente manipolabile per mostrare linee mediocri che funzionavano con efficienze fino al 150%.
Qui sta il potere dell'OEE. Quando viene scomposto nei suoi tre componenti principali, l'OEE riesce a rintracciare dove abbiamo perso la produzione. Ogni giorno in cui operiamo al 50% di OEE, possiamo perdere unità in modi diversi, e ogni perdita ha la sua propria struttura di costo.
Perdere 14.400 prodotti perché la macchina ha funzionato perfettamente, senza perdite di qualità ma a metà della velocità massima, è completamente diverso dal produrre 28.800 prodotti a piena velocità, per poi scartare 14.400 prodotti fuori specifica.
L'efficacia consiste nel:
Fare la cosa giusta - il prodotto corretto alla velocità corretta (Prestazione)
Farla nel modo giusto - senza rilavorazioni, difetti o sprechi (Qualità)
Farla al momento giusto - produrre come pianificato, mantenendo la macchina in funzione, minimizzando le perdite di tempo (Disponibilità)
Analisi Dettagliata dei Componenti
Disponibilità
Tornando all'esempio delle bottiglie, analizziamo una giornata tipica. Un turno standard dura 480 minuti. I nostri operatori fanno 10+30+10 minuti di pause, effettuano 2 cambi formato da 35 minuti ciascuno e perdono 60 minuti per fermi macchina durante il turno. Il resto del tempo la macchina è in modalità operativa.
Pause = 50 minuti Cambi formato = 70 minuti Fermi macchina = 60 minuti Totale = 180 minuti di tempo perso
Questo significa che abbiamo perso 180 minuti e ne rimangono solo 300 per essere efficaci. Anche se funzionassimo per il resto del tempo a piena velocità senza perdite di qualità, non potremmo mai essere più del 62,5% efficaci durante questo turno. Questo rapporto lo chiamiamo 'Disponibilità' o come viene utilizzato il tempo.
Prestazione
Supponiamo che il nostro sistema di confezionamento abbia un tempo ciclo ideale di 1 secondo per bottiglia, ovvero 60 bottiglie al minuto. Nei 300 minuti rimanenti, la macchina potrebbe produrre 18.000 bottiglie. Se alla fine del turno la macchina avesse prodotto 18.000 bottiglie durante il tempo di funzionamento, avrebbe performato al 100% della velocità. Se la produzione fosse stata più lenta, diciamo con un tempo ciclo di 1,5 secondi, la velocità massima si sarebbe ridotta di 2/3, e quindi la sua prestazione sarebbe diventata del 66,7%. L'output effettivo al 66,7% di prestazione è di 12.000 bottiglie.
Qualità
Se delle 12.000 bottiglie prodotte, 3.000 fossero fuori specifica, il tasso di qualità sarebbe del 75%. In termini di tempo, questo equivale a 50 minuti persi per problemi di qualità.
L'OEE Finale
In altre parole, abbiamo perso:
180 minuti per non funzionamento
100 minuti per funzionamento lento
50 minuti per la produzione di scarti
Il risultato è che la linea ha prodotto per 150 minuti in modo perfetto, alla giusta velocità e con la giusta qualità.
Teoricamente avremmo potuto produrre 28.800 bottiglie. Alla fine c'erano 9.000 bottiglie vendibili, quindi l'Overall Equipment Effectiveness era del 31,25%.
Disponibilità (62,5%) x Prestazione (66,7%) x Qualità (75%) = 31,25%
Il Tempo è Denaro
L'OEE è puramente basato sul tempo, ma poiché 1 tempo ciclo equivale a 1 bottiglia, l'OEE può essere calcolato in bottiglie per facilità d'uso. La maggior parte degli operatori non dirà "Oggi ho lavorato con un tempo ciclo di 1,5 secondi" ma piuttosto "oggi ho prodotto 40 pezzi al minuto" - che è la stessa cosa. Allo stesso modo, "Mi sono fermato per 5 minuti" equivale a "Ho perso 200 potenziali bottiglie che avrei dovuto produrre".
Applicazione Pratica dell'OEE
Sebbene i concetti siano relativamente semplici, le loro definizioni e applicazioni sono variate considerevolmente nel tempo, impedendo la possibilità di utilizzarli come benchmark e strumenti di performance all'interno e tra stabilimenti, per non parlare tra aziende diverse. L'obiettivo è presentare una definizione comune e un formato diretto per portare a un approccio chiaro e condiviso.
L'OEE dovrebbe essere analizzato su periodi significativi, tipicamente non meno di una settimana (10.080 minuti) o idealmente un mese (circa 43.800 minuti). Questo permette di ottenere dati statisticamente rilevanti per il processo decisionale.
È importante includere nell'analisi tutte le attività che fanno parte del processo produttivo, comprese le manutenzioni preventive, i cambi formato, la pulizia e/o la sanificazione. In passato, alcune aziende hanno cercato di nascondere queste attività considerandole come tempo non programmato, ma in realtà sono parte integrante della natura del processo produttivo.
L'OEE e il Costo della Qualità
Il "Costo della Qualità" non è il prezzo per creare un prodotto o servizio di qualità, ma il costo di non creare un prodotto o servizio di qualità. Ogni volta che il lavoro viene sprecato, si verifica una perdita che fa aumentare il "Costo della Qualità".
L'OEE fornisce una finestra chiara e potente sulla capacità di sostenere una produzione di qualità, mostrando come disponibilità (tempo), qualità (prodotto buono) e prestazioni (velocità) interagiscono. La parte delle Perdite è la frazione del tempo che viene persa a causa dell'incapacità del processo produttivo di essere coerente e sotto controllo.
Conclusione
L'OEE non è solo un indicatore numerico, ma un potente strumento di analisi e miglioramento. Utilizzato correttamente, può guidare le decisioni strategiche e operative, portando a un'ottimizzazione continua del processo produttivo. La chiave è comprendere che dietro ogni numero ci sono opportunità di miglioramento e che ogni miglioramento, per quanto piccolo, contribuisce all'eccellenza operativa complessiva.
ing.Gianluca Zorzan
Consulenza per l'automazione industriale,robotica, PLC.
Contatti
Richieste
info@gianlucazorzan.com
392-2605561
© 2024. All rights reserved.